Health Sciences and College of Engineering Team Up to 3D Print Medical Masks
Sleep and critical care expert Sairam Parthasarathy, MD, is uniquely positioned to help engineers design and test 3D-printed medical masks.
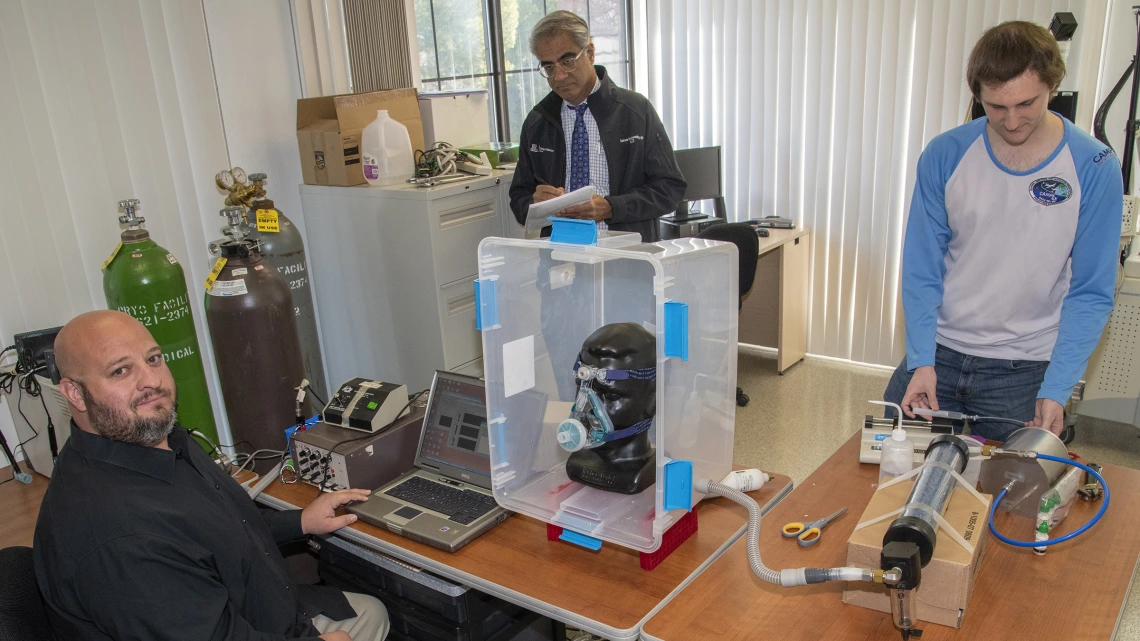
Lab manager Christopher Morton, Sairam Parthasarathy, MD, and engineering graduate student Connor Stahl test face masks in the Center for Sleep and Circadian Sciences.
Amid the COVID-19 pandemic, hospitals across the world are running short on personal protective equipment including N95 respirators — masks that, unlike surgical masks, fit tightly around the face and are capable of filtering out 95% of airborne particles.
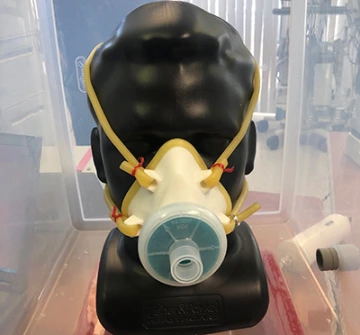
An early hybrid 3D-printed prototype face mask.
In response to the shortage, a group of researchers at the University of Arizona and UArizona Health Sciences is working to design, 3D print and test masks for health care workers at Banner – University Medical Center in Tucson.
The team includes Sairam Parthasarathy, MD, from the College of Medicine – Tucson's Department of Medicine, and three faculty members from the College of Engineering: Doug Loy, PhD, and Krishna Muralidharan, PhD, of the Department of Materials Science and Engineering, and Armin Sorooshian, PhD, of the Department of Chemical and Environmental Engineering.
The project includes iterative design, printing and testing phases, which are happening at a rapid pace. Dr. Loy and Dr. Muralidharan are leading the design and printing of the masks. Dr. Parthasarathy and Dr. Sorooshian, who studies aerosol particles in the atmosphere, test how well the masks keep out harmful biological particles and ensure they meet National Institute for Occupational Safety and Health standards.
Two weeks ago, Dr. Parthasarathy, director of the Health Sciences Center for Sleep and Circadian Sciences, had never met Dr. Loy, Dr. Muralidharan or Dr. Sorooshian, and wasn’t aware of efforts at the College of Engineering to design and 3D print personal protective equipment.
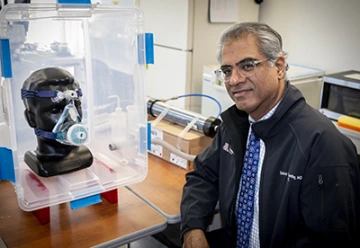
Sairam Parthasarathy, MD, pictured with an early mask prototype, is independently working on a mask that utilizes FDA-approved parts.
“I felt like I was primed for this,” said Dr. Parthasarathy, who has worked on bench test validations for more than 15 years.
His lab, equipped with an artificial lung simulator, provided an ideal location to test the prototype of the mask developed by Dr. Loy and Dr. Muralidharan, and Dr. Parthasarathy was able to contribute to the mask design and functionality, too.
There are two parallel universes in terms of mask use and design, Dr. Parthasarathy explained.
“One in the sleep center for patients, one in the ICU for workers — the two shall never meet. But now is an opportunity to make them meet, isn't it?” he said.
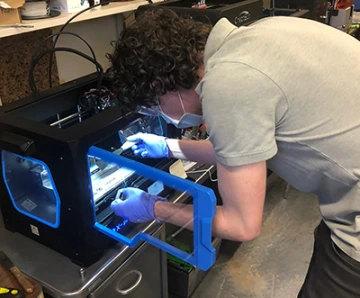
Engineering graduate student Kevin Frederick 3D prints mask components using a filament printer as part of the prototyping process.
With the new 3D printers on their way thanks to funding from the College of Engineering and the materials science engineering department, the team hopes to start producing masks within the next two weeks. The printers are all equipped with cameras and Wi-Fi control, so the process can be almost entirely automated, allowing researchers to follow physical distancing guidelines. Once they settle on an optimized mask design, they plan to make it open-source so others can print masks, as well.
“They say necessity is the mother of invention,” Dr. Parthasarathy said. "This is an example of how there are pockets of support and resident expertise from Engineering and Health Sciences. We've never worked together before, and this is sort of a dream team. It's very satisfying that we are collaborating to protect our health care workers.”